Corrosion Control Revolution: Discover The Ultimate Solution For Industrial Surfaces
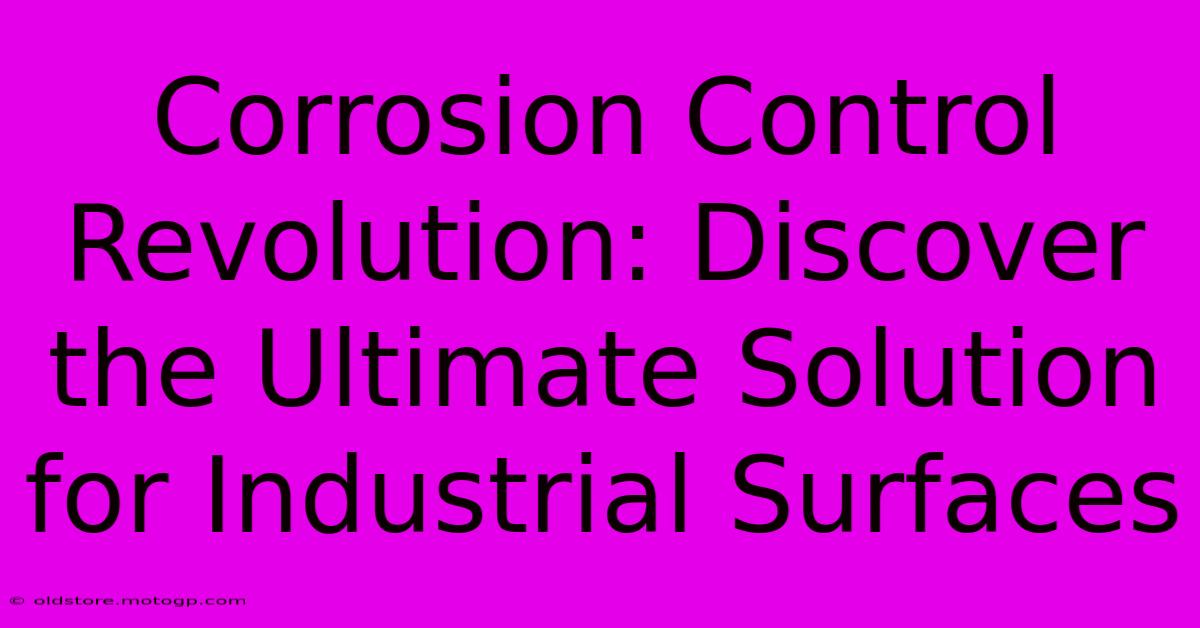
Table of Contents
Corrosion Control Revolution: Discover the Ultimate Solution for Industrial Surfaces
Corrosion. The silent destroyer of industrial infrastructure. It's a costly problem, leading to equipment failure, downtime, safety hazards, and significant financial losses. But what if there was a way to significantly reduce, or even eliminate, this ongoing threat? This article delves into the latest advancements in corrosion control, exploring the ultimate solutions for protecting your valuable industrial surfaces.
Understanding the Enemy: Types and Causes of Corrosion
Before we delve into solutions, understanding the enemy is crucial. Corrosion isn't a single entity; it manifests in various forms, each with its own contributing factors:
- Uniform Corrosion: This is the most common type, where the material deteriorates evenly across its surface. Factors like exposure to moisture and oxygen play a significant role.
- Pitting Corrosion: Localized corrosion attacks result in small holes or pits, often leading to unexpected failures. Chloride ions are frequent culprits.
- Galvanic Corrosion: Occurs when two dissimilar metals are in electrical contact in the presence of an electrolyte (like seawater). The more active metal corrodes preferentially.
- Crevice Corrosion: Concentrated corrosion within narrow spaces or crevices, where oxygen depletion and stagnant solutions promote corrosive reactions.
- Stress Corrosion Cracking: A combination of tensile stress and a corrosive environment leading to cracking and failure.
These different forms of corrosion require tailored solutions. Understanding the specific type impacting your industrial assets is the first step toward effective control.
Revolutionary Corrosion Control Methods: Beyond Traditional Approaches
Traditional methods, like painting and galvanizing, offer some protection, but they often require frequent maintenance and may not provide sufficient long-term solutions in harsh environments. The revolution in corrosion control lies in advanced technologies that offer superior durability and effectiveness:
1. Advanced Coatings: The Next Generation of Protection
Modern coatings are far more sophisticated than their predecessors. We're seeing the rise of:
- High-Performance Epoxy Coatings: Offering exceptional chemical resistance and durability.
- Polyurethane Coatings: Known for their flexibility, abrasion resistance, and excellent UV protection.
- Ceramic Coatings: Provide exceptional heat and chemical resistance, ideal for high-temperature applications.
- Specialty Coatings: Tailored coatings incorporating inhibitors or other additives to provide enhanced protection against specific corrosive agents.
The selection of the right coating depends heavily on the specific application and the type of corrosion anticipated.
2. Cathodic Protection: A Proven and Effective Technique
Cathodic protection (CP) is an established electrochemical method that prevents corrosion by making the metal surface cathodic. This involves supplying a current to the metal structure, either through sacrificial anodes or impressed current systems. CP is particularly effective in submerged or buried structures.
3. Corrosion Inhibitors: A Chemical Approach to Prevention
Corrosion inhibitors are chemicals added to the environment to reduce the rate of corrosion. These substances can form a protective film on the metal surface, neutralize corrosive agents, or interfere with electrochemical reactions. The choice of inhibitor depends on the specific corrosive environment and the material being protected.
4. Material Selection: Designing for Durability from the Start
Choosing corrosion-resistant materials is a fundamental aspect of corrosion control. Stainless steels, nickel alloys, and other specialized alloys offer inherent resistance to various corrosive agents. Proper material selection, considering the specific environment, can significantly reduce the need for other corrosion control methods.
Implementing a Comprehensive Corrosion Control Strategy
Effective corrosion control isn't a one-size-fits-all solution. A comprehensive strategy requires a multi-faceted approach:
- Regular Inspection and Monitoring: Early detection of corrosion is crucial. Regular inspections help identify problems before they escalate into significant damage.
- Environmental Control: Minimizing exposure to corrosive agents, like moisture and salts, through proper ventilation, drainage, and cleaning, is a proactive approach.
- Maintenance and Repair: Prompt repair of any detected corrosion is essential to prevent further damage and extend the lifespan of your assets.
Conclusion: Securing Your Industrial Future
Corrosion is an unavoidable reality in many industrial settings, but it doesn't have to be a crippling expense. By implementing a comprehensive corrosion control strategy that incorporates the latest advancements in coatings, cathodic protection, inhibitors, and material selection, you can significantly extend the life of your industrial assets, reduce downtime, enhance safety, and ultimately safeguard your bottom line. The ultimate solution is a proactive and integrated approach tailored to your specific needs and environmental conditions. Invest in corrosion control – it's an investment in the future of your business.
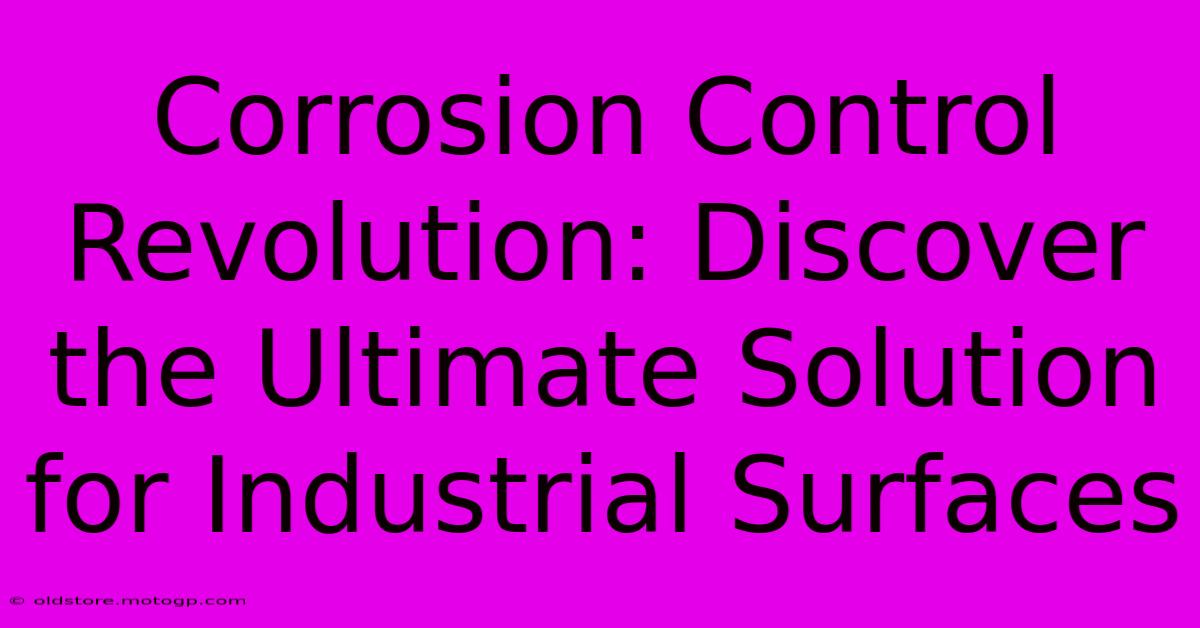
Thank you for visiting our website wich cover about Corrosion Control Revolution: Discover The Ultimate Solution For Industrial Surfaces. We hope the information provided has been useful to you. Feel free to contact us if you have any questions or need further assistance. See you next time and dont miss to bookmark.
Featured Posts
-
Master Zone Lighting Unlock The Secrets Of Ambiance And Functionality
Feb 07, 2025
-
Churchills Pact With The Underworld A Devilish Alliance For Victory
Feb 07, 2025
-
A Path To Purpose Unlocking The Essence Of Christian Identity
Feb 07, 2025
-
The Ultimate Guide To Jotun Price 2024 Unraveling The Hidden Truth
Feb 07, 2025
-
Groovy And Functional The Coolest Retro Appliances On The Market
Feb 07, 2025