Molding/Moulding
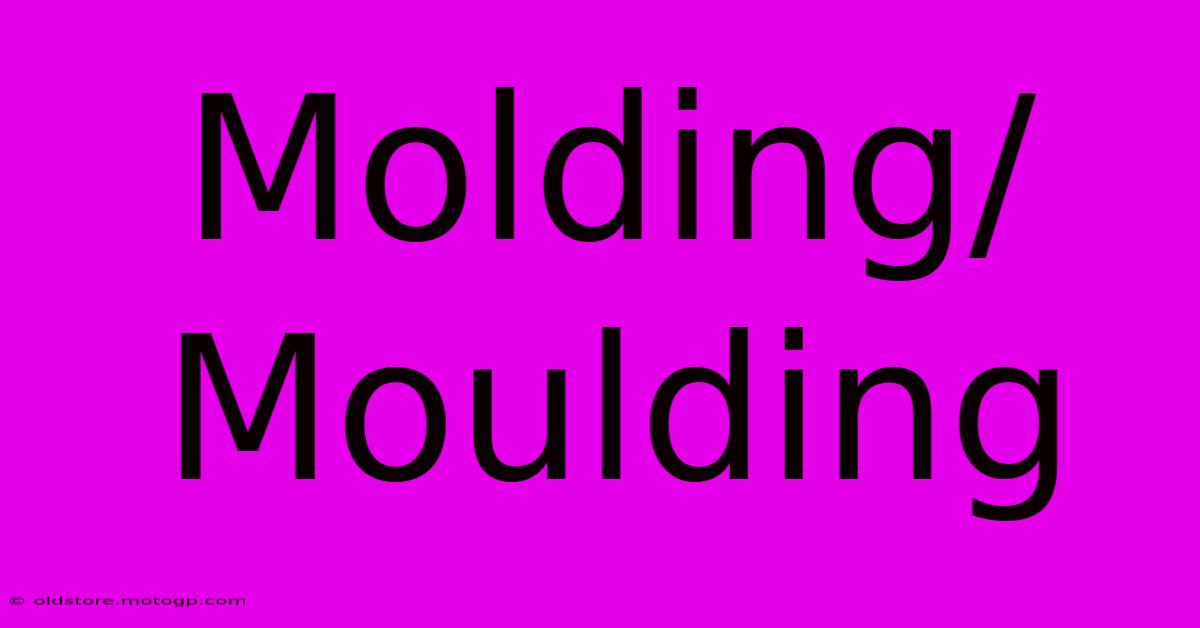
Table of Contents
Molding/Moulding: A Comprehensive Guide to Processes, Materials, and Applications
Molding, or moulding (the spelling varies depending on region), is a manufacturing process used to create objects of a specific shape by pouring or pressing a fluid material into a mold or mould (again, spelling varies). This encompasses a vast range of techniques used across numerous industries, from automotive parts to intricate jewelry. This comprehensive guide will delve into the diverse world of molding, exploring its various types, materials used, and widespread applications.
Understanding the Molding Process: Key Principles and Variations
At its core, molding involves three key steps:
-
Mold Preparation: A mold, a cavity of the desired shape, is meticulously prepared. This often involves intricate design and construction, depending on the complexity of the final product and the chosen molding method.
-
Material Introduction: The chosen material, in liquid or semi-liquid form, is introduced into the prepared mold. This can be achieved through injection, casting, pressing, or other methods, varying significantly based on the type of molding employed.
-
Curing and Demolding: The material is allowed to cure or solidify within the mold. Once cured, the finished product is carefully removed from the mold. The ease of demolding depends on the mold design, material properties, and the employed technique.
Different Types of Molding Processes
The realm of molding encompasses a wide array of processes, each suited to specific materials and applications. Some prominent examples include:
1. Injection Molding:
- Description: A highly automated process where molten plastic is injected into a closed mold under high pressure. It's ideal for mass production of identical parts with high precision.
- Materials: Thermoplastics and thermosets.
- Applications: Automotive components, electronics housings, packaging, toys.
2. Compression Molding:
- Description: Material is placed in a heated mold and compressed until it cures. Suitable for producing large, complex parts.
- Materials: Thermosets, rubber, and some composites.
- Applications: Large plastic parts, fiberglass components, rubber seals.
3. Rotational Molding:
- Description: Powdered or liquid plastic is placed in a heated mold that rotates on two axes, distributing the material evenly across the mold's interior surface.
- Materials: Plastics, elastomers, and some composites.
- Applications: Large hollow parts like tanks, kayaks, and playground equipment.
4. Vacuum Forming:
- Description: A sheet of thermoplastic is heated and then drawn into a mold using a vacuum. This is suitable for producing shallow, large-area parts.
- Materials: Thermoplastics such as acrylic, polystyrene, and PVC.
- Applications: Packaging, signage, and some medical devices.
5. Casting:
- Description: Liquid material is poured into a mold and allowed to solidify. Casting techniques span various materials beyond plastics.
- Materials: Metals, resins, concrete, plaster.
- Applications: Sculptures, metal parts, jewelry, dental models.
Common Molding Materials
The choice of material directly impacts the final product's properties, cost, and application. Some frequently used materials include:
- Plastics: Thermoplastics (e.g., polypropylene, polyethylene, ABS) and thermosets (e.g., epoxy, polyester).
- Metals: Aluminum, zinc, magnesium, and other alloys.
- Rubber: Natural rubber and various synthetic rubbers.
- Composites: Materials combining multiple components for enhanced properties (e.g., fiberglass-reinforced plastics).
Applications Across Industries
Molding's versatility makes it a cornerstone technology across diverse sectors:
- Automotive: Parts for cars, trucks, and other vehicles.
- Electronics: Housing for computers, smartphones, and other devices.
- Medical: Prosthetics, implants, and medical devices.
- Aerospace: Components for aircraft and spacecraft.
- Packaging: Bottles, containers, and other packaging materials.
Choosing the Right Molding Process: Key Considerations
Selecting the appropriate molding process involves careful consideration of several factors:
- Part complexity: Simple parts may be suitable for simpler processes like vacuum forming, while intricate designs may require injection molding.
- Production volume: Mass production often favors automated methods like injection molding.
- Material properties: The chosen material's characteristics (e.g., melting point, viscosity) dictate the applicable molding techniques.
- Cost: Each process carries varying costs associated with tooling, material, and labor.
Conclusion:
Molding is a fundamental manufacturing process with immense versatility. Understanding the different types of molding, materials, and applications empowers engineers and manufacturers to select the optimal approach for their specific needs, paving the way for innovative product development and efficient manufacturing solutions. From the simplest plastic toys to sophisticated aerospace components, molding plays a crucial role in shaping our modern world.
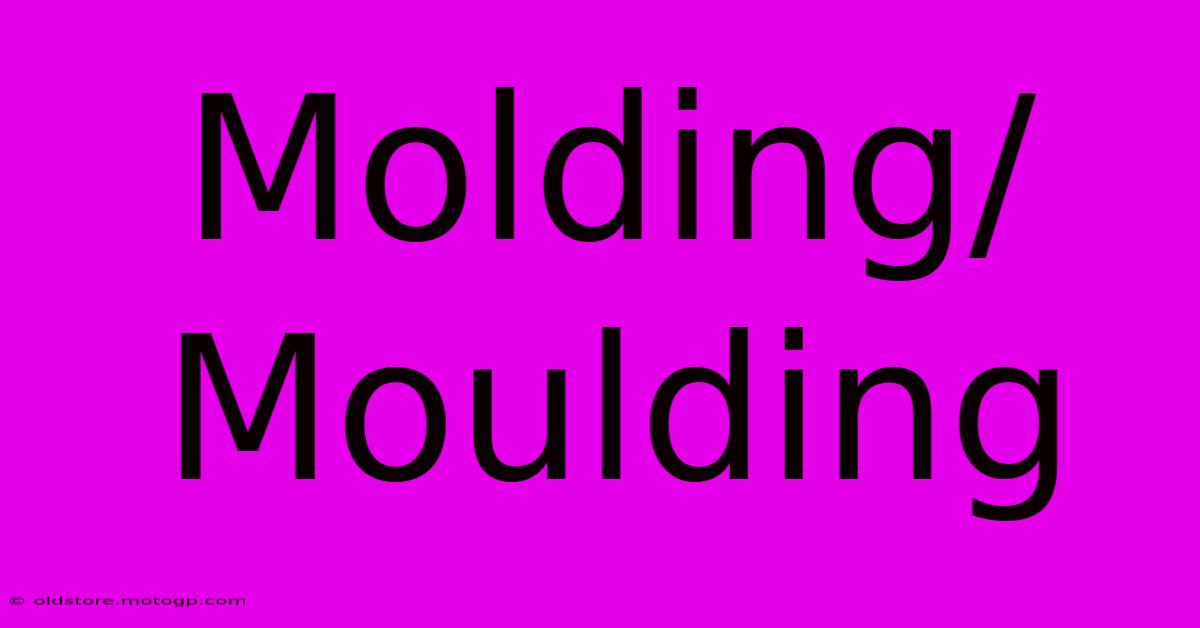
Thank you for visiting our website wich cover about Molding/Moulding. We hope the information provided has been useful to you. Feel free to contact us if you have any questions or need further assistance. See you next time and dont miss to bookmark.
Featured Posts
-
Unveiled The Hidden Wisdom Of Trees That Will Transform Your Life
Mar 12, 2025
-
Transform Note Taking Into An Art Form With Custom Small Notebooks
Mar 12, 2025
-
Forest Freshies Bring Natures Green Sanctuary Indoors
Mar 12, 2025
-
Art Alchemy The Ultimate Guide To Fixatives For Every Medium
Mar 12, 2025
-
Prepare For A Shopping Bonanza Jc Penney Eastpoint Mall Unveils Unmissable Sales
Mar 12, 2025